Turbine Rocket Saucer
please see links above for later
flights
Click on any picture to enlarge |
Original design -
spinning, clustered saucer with LED lighting
Flown on 4 to 8 motor clusters of 24mm motors, mostly Estes D11-Ps
20 inches diameter. Flight weight 1.3 to 2.0 pounds. |
Videos: 2012
flights video 2011 flights video 2010
flights video More
info: 2012 flights
2011 flights Rocketry Forum
thread
3 Cool night flights in 2012
flights video and one more in 2011 flights video
Fired by Rocketflite
igniters and Cluster Box |
2010 flights Turbine Rocket Saucer is featured in the Dec/Nov 2011 issue of Sport
Rocketry
Flight 15: 6x D11-P motors.
Awesome light effects and shower of flame and sparks!
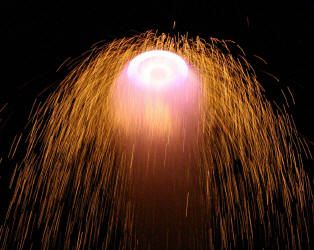 |
Turbine Rocket Saucer stats for first year of flight - 2010:
> Original design built spring 2010
> Flown 15 flights firing all 74 motors loaded
> All motors 24mm Estes BP, mostly D11-Ps
> Flown on 4, 6 or 8 motors, seems to do best on 6
> Always fired by Rocketflite MF igniters
> Always
used high output cluster box |
Flights 13-15: 11/21/10
CMASS Amesbury, MA
Last CMASS launch of the season and an
opportunity for night flights.
The LEDs worked great! |
|
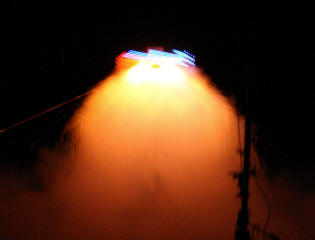
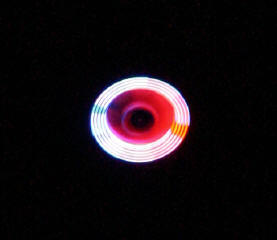
Flight 14: Flew on 6x D11-Ps and the effect
was wild!
To the eye the saucer appeared as smooth white rings above a huge shower of
flame and sparks.
These pictures offer another opportunity to estimate saucer RPM.
Images were
taken at 1/45 sec exposure, ISO 1600, in a continuous
series at 3 per second.
> Fifth picture was at 5 second onto the flight and colors overlap about 1/3
rotation (in 1/45 sec) so 15 rev per second x 60 = 900 RPM.
> Fourth picture is at 4 seconds onto flight and colors overlap almost 1/2
rotation so about 20 rev per second x 60 = 1200 RPM.
> Third picture is at tail end of motor burnout, end of effective motor
thrust is about 1.6 seconds. With the loss of 300 RPM from second 4 to 5 and
peak RPM at 1.6 seconds, I estimate roughly 2000 peak RPM.
2000 RPM estimate for 6x D11-Ps fits reasonably well with 1500 RPM estimate
for 4x
D11-Ps. |
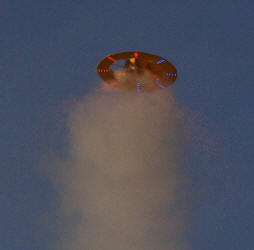 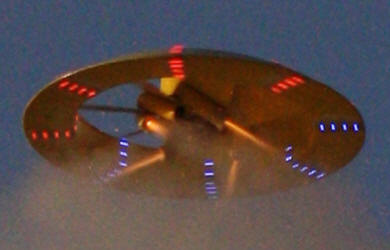
Flight 13: Went up near dusk on 4x D11-P motors. Due to
the 3oz weight added for lighting, altitude was slightly reduced to about
100ft.
To the eye, the red and blue LEDs blended to a smooth purple series of
rings.
These pictures were taken at 1/3000 second exposure.
The fourth picture is at the end of the engine burn and offers an
opportunity to roughly estimate saucer RPM:
> I estimate that the smearing or stretching of the LED light in the image
reaches about 1/15 of the way to the next band of lights.
> The next band of lights is 1/8 of the way around the saucer.
> So the saucer completed 1/15 x 1/8 = 1/120 of a rotation in the 1/3000
second exposure. 3000/120 = 25 rev per second x 60 = approximately 1500 RPM |
Flights 11-12: 11/6/10
CMASS Amesbury, MA Two more good flights on 4x D11-P
motors. |
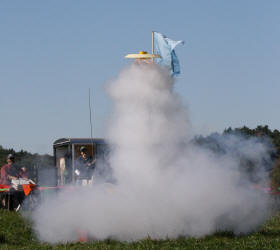
Flight 10:
10/2/10 CMASS Amesbury, MA
Nice flight on 6x D11-P
motors.
|
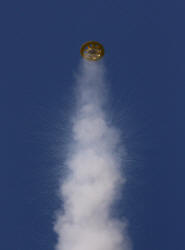 |
|
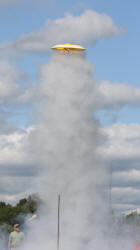
Flight 9:
9/18/10 Got in another flight on a beautiful day at CMASS in
Amesbury, MA.
Loaded up the Turbine Rocket Saucer with 8x D11-P motors and sent it up
on a column of smoke and fire. With the 8 motors in the highly canted
motor mounts, the rocket spun so fast it stripped off two of its motors
in flight. As these two motor mounts were opposite each other, I left
them off and now fly the rocket with 6 motors very nicely.
Also had the privilege of flying Carl Tulanko's beautiful, huge upscale
Tres that day:
http://www.rocketryforum.com/showthr...306#post133306 |
 |
|
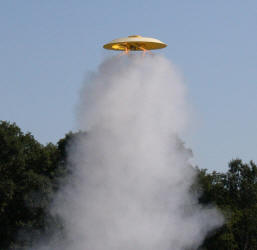
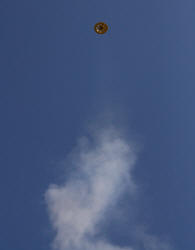
Flights 6-8: 8/28/10 CMASS Acton, MA
All on 4x D11-P clusters with same great flight profiles as previous
flights.Pictures of first launch of
the day: The intense heat and sparks of the Rocketflite ML igniters is
evident in the first picture.
The fast spinning rocket with its spikes of flame seems to be sitting above
the column of smoke.
Interesting smoke starburst effect at the end of the burn. Rocket continues
to lift and briefly hover after the burn. |
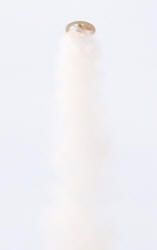
Flights 3-5: 8/14/10 Turbine Rocket Saucer flew
three times at the CMASS launch in Acton, MA.
Each of the 3 flights went up on 4 motors all loaded in the new motor tubes
which are canted at 60 degrees from vertical.
The flights were great, with lots of spin and safe, quick, straight
liftoffs.
Recoveries were gentle this time due to increased spin and moderate
altitude, estimate about 100 ft.
flight 3 - 4x D12-0 (pictured)
flight 4 - 2x D12-0 and 2x E9-4
flight 5 - 2x D12-0 and 2x E9-4
This is the flight profile I was hoping for! Spinning liftoff, hover and
gentle recovery.
From the video it looks like about 4 seconds of lift, 3 seconds hover and 5
seconds for gradual recovery. |
Flights 1-2: The only shortcoming in both
flights was on the way down. Rocket continued to spin at a gradually slowing
rate until it hit the ground, so the gyroscopic effect prevented it from
flipping over the way most saucers do on recovery. Instead it tipped to
about a 45 degree angle and came down on one edge, requiring some repair.
After these two flights, added more motor tubes that were highly canted as
noted in the August section of the build at the bottom of this page.
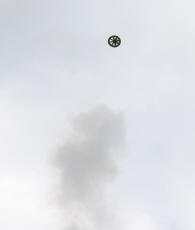
Flight 2: 7/31/10 Second flight liftoff on 8x D12-0 motors was
great, firing all motors, with quick spin and lift off the rod.
Very similar flight behavior to previous flight, this time reaching
150-200ft altitude.
Last picture shows the continued lift after motor burnout.
Both times liftoff was straight up and recovery angled to about 45 degrees,
landing downwind.
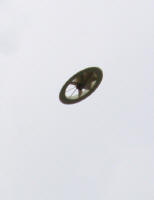
Flight 1: 7/31/10 First flight
liftoff on 4x D12-0 motors was great, firing all motors, spinning and
lifting quickly off the rod.
Gyroscopic effect was noticeable with
rocket staying very flat during liftoff. Some moderate lift continued after
motor burnout due to turbine action of fins. Estimate about 100-150ft
altitude. |
Build -
2010
July - initial build August - added more motor tubes
and fiberglass
November - added LEDs
Click on any thumbnail to see a picture more closely |
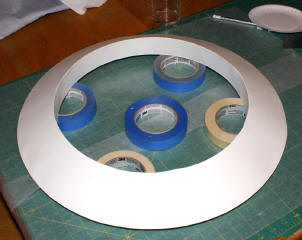
I had long wanted to design and build a spinning, saucer-style rocket,
inspired by Applewhite's saucers
and FlisKits' Frick-n-Frack.
If it works, it will look cool, benefit from gyroscopic stabilization, and
with the right use of fins, convert some of that spin into lift.
Outer rim is shaped and built like several Applewhite saucer designs. 20"
total OD, 3" wide with 30 degree angle between top and bottom.
Ring uses 1/4" foam board for the bottom and paper to form inner and top
rings. |
Fiberglassed outer ring lightly for strength using 1.3 oz glass.
Original build had 3 layers on the inside diameter as that is what the
"turbine" blades will mount to,
2 layers on the top and 1 layer on the bottom of the foam board to harden
the surface. |
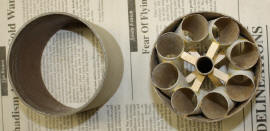
Eight 3" x 3/16" basswood fins form inner turbine blades. Made a diagram to
assist in accurate placement of all components.
Airfoiled 8 fins and tacked them in place with CA before applying light
epoxy fillets top and bottom.
Center is 4" tube that
accepts interchangeable motor mounts. This tube is 3" long and wrapped with
a couple layers of 1.3 oz FG.
Motor mount unit has 8x 24mm tubes canted about 20 degrees from vertical,
surrounding 1/2" rod lug.
This will allow many motor combinations and for the saucer to start rotating
before separating from the rod. |
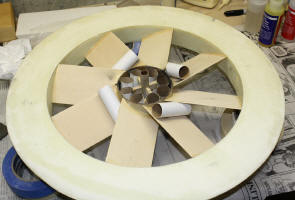
August - After hard landings in the first two
flights split a section of outer edge, painted epoxy (West 206) inside the
tear, taped it together and applied weight to press the bottom flat. Then
added slightly more fiber glass to top and bottom of outer ring, bringing
build up of all 3 sides up to 3 layers of 1.3oz. Saucer weight went from
13.3oz to 14.9oz after this step.
Finally added 4 more motor tubes mounted to inner area of fins. These new
motor mounts are canted at 60 degrees from vertical.
Later on, an additional four very canted motor mounts are added. Original 8
center motor tubes are canted at 20 degrees from vertical.
With more ring weight and strength, as well as very canted motor mounts,
goal is to keep the saucer spinning fast and flat until it returns to
ground. Altitudes will be moderate. |
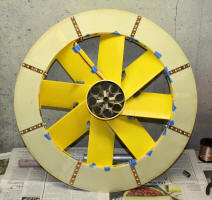
November - In anticipation of a night flying
opportunity LEDs were added to the TRS.
LED strips as purchased have
60 LEDs on a 40 inch strip that can be cut at any 2" increment.
They are rated at about 150mA (for 60 LEDs) at 12V.
Picked up a 11.1V 480mAh Lipo battery that weights only 1.4 oz.
Cut LED strips into 8"
sections and used the sticky backing they came with to apply them to the
saucer. Strips wrap from the center on ring ID (both ends near saucer outer
edge) to help the LEDs to hold despite very strong centrifugal forces.
Removed a clear, protective silicone covering on the strips, both to bend
them as sharply as required and because centrifugal force would have
stripped them off anyway.
Soldered power wire from strip to strip around the ring ID, ending in a
battery terminal near the center. Then painted LED strips and all wiring
with two coats of West 206 epoxy to harden and adhere. Went with one side
red and one side blue to maximize visibility of spinning effect in flight.
There are 96 LEDs on this total and the amount of light it throws off is
surprising.
I am very pleased with the results and look forward to flying with lights on
both day and night going forward.
good news: Complete battery and light system added only 3oz to the rocket.
bad news: LEDs cost $50 and battery $30.
In theory the 480mAh battery will power the 240mA load for 2 hours. To
preserve the battery will only use a fraction of this before recharging.
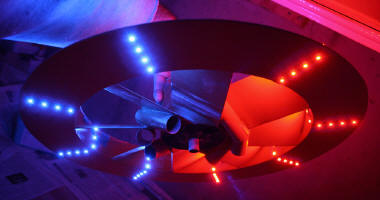 |